Whether constructed of steel or aluminum, metal yachts deserve a second look
In the 1960s and early 1970s we rarely saw metal yachts in North American waters. Steel yachts had been built in Holland and Germany for many years but, with only oil-based paints to protect them, they were not particularly long lived. Indeed, I’ve seen lovely 40-foot steel yachts corroded to junk in 10 to 12 years. A few custom aluminum yachts were built overseas as well and in a couple of quality yards in the U.S. However, aluminum was considered to be a material restricted to large and expensive craft; half the weight for twice the price was the popular conception. Today however, due to advances in the protection of steel hulls and the reduction in the cost of aluminum, metal is often the material of choice for both custom-built and amateur-built yachts, so steel and aluminum craft are commonly seen in almost every harbor.
Each material has its advantages, but the racing skipper will choose aluminum construction for its combination of lightness and strength, of course. The cruiser, on the other hand, may prefer steel for its greater strength and lower initial cost, or aluminum for its longevity, low maintenance, and high resale value. Sailors interested in a metal yacht need to know the pros and cons of the two materials so they can make an intelligent choice, whether buying a used boat, building their own, or having a new custom yacht built. I offer a few points to consider.
|
Weight
The simplest comparison is that aluminum weighs about 168 pounds per cubic foot and steel weighs 490 pounds per cubic foot, almost three times as much. It is not that simple a comparison though. The machinery, interior furnishings, hardware, rig, general equipment, and stores weigh about the same for steel and aluminum craft, so the overall weight advantage of an aluminum yacht is not nearly as great as it might seem.
Strength
Comparing strengths is made more difficult because aluminum alloys lose strength after welding while steel does not. The table below shows the differences between some typical alloys.
Steel’s strength advantage seems obvious, but it is normal practice to increase the scantling of an aluminum part to make up for its lower strength. For example, a steel 40-footer would be plated with .140-inch-thick steel, giving a tensile strength of .140 x 58,000 = 8,120 pounds per inch of plate. Her aluminum sister might be plated with .1875-inch-thick material, giving a strength of .1875 x 39,000 = 7,312 pounds per inch of plate. The 10 percent difference in strength is relatively inconsequential while the thicker aluminum still has a substantial weight advantage: 2.63 pounds per square foot of hull compared to 5.72 pounds per square foot for the steel yacht, less than half the weight of steel.
However, as pointed out earlier, the overall weight advantage might be only 20 to 25 percent in the long run due to the weight of the other parts of the yacht. Still, that means the aluminum yacht can be 20 percent lighter or carry extra ballast, and that translates into improved performance.
Steel also has the advantage of being 60 percent harder than aluminum, so it is much more resistant to abrasion in a grounding on rock or rubbing up against a concrete bulkhead. And, it is more malleable, so it will stretch farther in a collision or a hard grounding on granite before rupturing. Aluminum, in turn, is more resistant to abrasion than either fiberglass or wood and will stretch a great deal more in a collision. In any case, I’m sure our readers will never allow their boats to get into a grounding or collision situation so this factor is not critical!
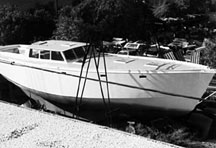
Brewer’s Alaska 43 is an example of a double-chine steel hull.
In the stretching category, I can tell of a 60-foot ultra-light aluminum design of mine that had her anchor chain slip the stopper while sailing into the teeth of a 50-knot squall, letting the anchor drop 15 feet or so before it jammed. For close to an hour the boat rose on each big sea and fell onto her heavy Bruce anchor, yet the only damage was several 2-inch-deep dents in her light .160-inch aluminum plating. This is certainly an unusual accident but shows one of the solid advantages of metal yachts. I feel certain a wood or glass hull would have suffered severe damage in a similar situation. In any case, sailing aboard a metal yacht can be very comforting when you are out on the deep blue competing for lebensraum with floating cargo containers.
Too, both steel and aluminum yachts are essentially one-piece structures without the annoyance of leaking hull/deck joints, leaking chainplates or other weak points. Even cleats and other hardware can be welded to the deck, or machine-screw fastened to pads welded in place, to avoid bolt holes through an otherwise watertight structure.
Corrosion
The marine aluminum alloys (5454, 5083, and 5086) used for yachts and commercial fishing vessels are very different from the aluminum used in your pots and pans at home. The marine alloys contain a substantial percentage (3.4% – 4.9%) of magnesium, depending on the specific alloy, and are highly resistant to corrosion in sea water. They are essentially inert. Indeed, these metals are not even similar to the 6061-T6 used in your mast. The latter is a heat-treatable alloy that loses substantial strength in the vicinity of a weld; hardly a quality we want in our hulls with their hundreds of feet of welding. Nor is 6061-T6 as corrosion-resistant in a marine atmosphere, as some sailors have discovered to their sorrow. Still 6061-T6 is favored for internal use by many builders due to its stiffness and is used, suitably increased in thickness, for frames, longitudinals, keel, knees, and other parts that will not come into contact with sea water. Quality aluminum yachts are plated with 5000 series alloys on the hull and superstructure, of course, and are all-welded structures.
Proof that the marine aluminum alloys are unaffected in sea water is that many commercial fishing craft, and an increasing number of yachts, are not even painted above the waterline. To paint or not to paint is solely at the owner’s discretion. The aluminum will darken to a gray color with age, but its strength and durability are essentially unchanged. The interior of the aluminum hull need not be painted either but, obviously, the bottom must have anti-fouling paint applied to prevent the growth of performance-robbing weeds and barnacles.
Steel, of course, rusts quickly in a saltwater atmosphere, so a steel yacht needs to be protected inside and out. The interior is usually painted with coal-tar epoxy, while the exterior can be epoxy-coated or flame-sprayed with zinc or aluminum. In either case, the steel must be sand-blasted inside and out with sharp silica sand to provide a tooth for the paint or flame spray. This substantial extra labor can offset the higher material cost of the aluminum to a substantial degree. In talking to a couple of builders recently I had one tell me that he would charge about 20 percent more for a completed aluminum yacht over steel and another say that aluminum and steel yachts come out very close in price due to the extra labor of blasting and finishing the interior of the steel hull.
The same disagreement arises when “experts” are asked about the benefits of flame spraying a steel hull to prevent corrosion. One advises to flame spray, preferably with aluminum; another says that an epoxy coating is better than flame spraying. I have seen both methods give good results after years of service and, in my opinion, it is simply up to the owner to toss the coin.
Whether steel or aluminum, both metals are well below copper on the galvanic scale, and using bronze or copper in contact with either is a no-no! Perhaps the epitome of this is the very famous designer who, early in this century, built a large and expensive racing yacht of aluminum plating on bronze frames. The vessel barely lasted a year, much to the surprise and dismay of the designer and owner!
So, no bronze seacocks, no copper bottom paint, and don’t drop any pennies in the bilge of an aluminum yacht! Some designers and builders use stainless steel seacocks, but I prefer the fiberglass-reinforced nylon type, as I do not like to see stainless steel used below the waterline in salt water if at all avoidable. For anti-fouling protection, tin-based bottom paint is the best available for metal yachts, the best available for any yacht for that matter, but is outlawed in many countries due to its toxicity. Paint manufacturers have come up with several alternatives, though, so some research will be necessary if there is a metal boat in your future.
Hull shape
Although European builders in the 1950s, and even earlier, had the skills necessary to build fully developed hulls, this ability was limited to a very few quality (read “expensive”) yards in North America. Thus, only chine hulls were readily available here and that, of course, was another reason that metal boats were not popular.
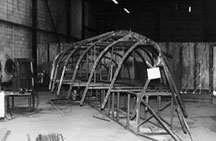
Peachy Keen, in various stages of development, shows Brewer’s radius bilge with straight frames above and below the radius bilge.
In the early 1970s we designed a 35-foot steel sloop called the Goderich 35 and used a shape that was, essentially, a single-chine hull with a very large radius at the chine. The radius started at the stern at about a 2-foot radius and increased as it progressed forward to 4 feet or more. I don’t know if we were the first designers to use this technique, but I had not seen it done before, so it is possible that we did originate it. In any case, the boat turned out quite well, a number were built and one 35, Globe Star, skippered by professor Marvin Creamer, circumnavigated the globe without instruments of any kind, using Creamer’s knowledge of currents, drift, winds, and other natural phenomena to locate his daily position. These methods proved surprisingly accurate and could have been known to the very early navigators.
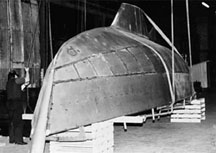
When plated, the radius bilge goes on in short sections while the flat areas are installed in long plates.
Shortly after the Goderich 35 appeared on the scene, other designers were coming out with radius-bilge hull designs and, in a few years, it was not at all uncommon to see radius-bilge steel yachts advertised as semi-production boats or bare-hull kits for home completion. The radius-bilge system caught on with aluminum boats as well, but a few builders were already beginning to turn out fully formed aluminum yachts as the softer 5000 series aluminum is somewhat easier to work with and form than steel. Today there are a number of good builders who can produce an excellent, fully formed aluminum hull, a few who can do the same in steel, and many who can do a fine job on a radius bilge hull in either metal.
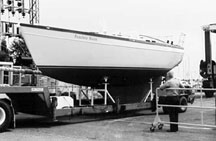
Ready to launch, the boat’s a beauty.
Miscellaneous advantages
Both metals have their own unique qualities, of course. Steel is easier to weld, especially under adverse conditions. Aluminum needs to be kept hygienically clean while under construction, and welding it requires considerable training and solid experience.
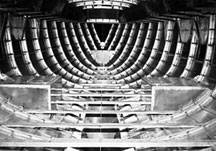
A look inside Troubador while under construction, shows the shining ribs and curved frames of a fully developed aluminum hull.
Aluminum is non-magnetic, so compass adjusting is easier and auto-pilots work better, at least in my experience. Steel is fireproof, while aluminum will melt if given enough heat, as the Brits found to their dismay in the Falkland Islands war. It is still more fireproof than wood or fiberglass, obviously. However, if everything else aboard the boat burns, having a hot metal hull afloat in the middle of the ocean may not be of any great comfort.
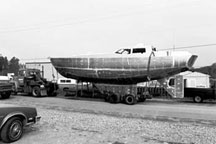
Troubador’s plating shows details of an elaborate construction process.
Built-in tanks work well in both materials and increase the tankage capacity substantially. The 5000-series aluminum water tanks do not need to be epoxy- or cement-coated inside to prevent corrosion. Some people say an aluminum water tank can cause neurological disorders (Alzheimer’s). I believe it can if you grind it up and eat it, but we still use our aluminum cooking pots and pans, and I would not hesitate to have aluminum water tanks on my boat. An unusual advantage of metal boats is that the built-in tanks are easy to repair. You simply cut a hole in the hull, repair the tank from the inside, and weld the hull back up again. It beats trying to wrestle a 50-gallon tank out of a 40-gallon opening so you can get at it to fix a bad leak.
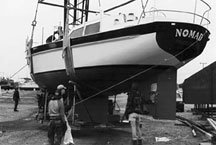
Nomad has an aluminum deck and house on a steel hull.
Emergency repairs on either material are fairly straightforward. Not as simple as repairing a wooden boat, perhaps, but certainly as easy as fiberglass. A repair patch can be quickly welded onto a steel hull and almost any out-of the-way port will have the necessary equipment to do it. Aluminum, on the other hand, can be readily drilled and tapped so an owner can fasten a gasketed patch in place until he can get to a port where aluminum welding facilities are available.
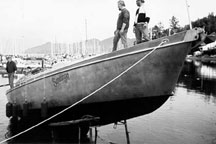
Sandingo is launched with unpainted aluminum topsides and deck.
Steel and aluminum each have distinct advantages. They can both be built by amateurs, and I have had fine yachts, from 30 to 60 feet, crafted in metal to my designs by competent amateurs as well as by professional yards. If the amateur can combine good welding skills with reasonable experience in metal fabrication, there is no reason why an excellent yacht cannot be produced at a reasonable cost. And now, with sound 20- to 25-year-old metal yachts occasionally available on the market, the older metal boats can take their place within the fleet of good old boats as well.
Further reading:
- Steel Boat Building, by Thomas E. Colvin, International Marine Publishing Co.
- Boatbuilding with Steel, by Gilbert C. Klingel, International Marine Publishing Co.
- Boatbuilding with Aluminum, by Stephen F. Pollard, International Marine Publishing Co.
Article from Good Old Boat magazine, July/August 1999.